Incubators have traditionally been a mainstay for most biological and life science laboratories, to grow or sustain biological cultures, reproduce germ colonies or breed/grow insects. The most basic incubators allow researchers to recreate strict temperature conditions for optimal growth, development and/or maintenance of finicky cells. Temperature homogeneity is also critical, as fluctuations in the living environment can be deadly.
As the fields of biotechnology and biopharmaceuticals have expanded, the demand for higher-precision incubators has increased. In addition, regulatory requirements regarding good-laboratory and -manufacturing practices (GLP and GMP) have been refined and intensified. Among other things, this has resulted in the advent of increased sophistication for cell culture control and monitoring. Additional instrument features means additional cost, leaving many lab managers wondering if all the bells and whistles are really necessary for their applications.
Practically speaking, shrinking laboratory budgets have left many labs seeking affordable options that do not compromise the results of their experiments. In regards to incubators with carbon dioxide sensors and controllers, the sample type will determine if it’s necessary, as some cell types depend on it for ideal development. Here are some points to consider:
Do I Need CO2 Control?
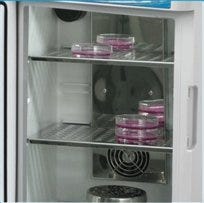
Benchmark Scientific’s myTemp™ Mini CO2 digital incubator
Incubators generally control user-specified internal temperature and humidity conditions. Another common feature is the ability to control carbon dioxide (CO2) to around 5%. This is important for two reasons: 5% CO2 closely simulates the physiological conditions that cells would experience within body systems, and functions as a critical pH buffer. In fact, pH levels within cultured cells are so important that most cell culture media contain indicators so that operators can visually identify dangerous shifts in pH. Animal cells in culture have been removed from their larger biological “host” (i.e., the organ), yet researchers want to obtain results that are most relevant to a living organism.
Thus, it is of paramount importance to control as many parameters as possible to mimic these conditions. Some biological labs working with bacteria such as E. coli, or single-celled eukaryotic cells like S. cerevisiae, do not require carbon dioxide control for optimal culture growth. Therefore, these labs will often opt for more economical incubators that only control temperature and humidity. However, if your laboratory is culturing cells or tissues from animals, the answer to the question “do I need CO2 control?” is most certainly ”yes.”
Controlling CO2 Levels: Thermal Conductivity or Infrared?
CO2 incubators typically offer the ability to specify the set-point for the carbon dioxide level (generally 5%). The incubator contains a CO2 sensor and a control module which prompts a flow of CO2 when levels fall. When the incubator door is opened, CO2 rapidly rushes out of the incubator chamber due to the difference in concentration with the outside environment. This drop is detected by the sensor and a relay transmits a signal to raise the carbon dioxide level. There are two common forms of detectors that are used for monitoring carbon dioxide levels within incubators: thermal conductivity and infrared.
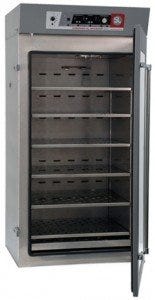
Humidified CO2 incubator with IR sensor from Shel Lab
Thermal-conductivity sensors measure variations in temperature resistance. In the incubator, one sensor is exposed to the chamber (the environment) while a second one is isolated (the control). Since a decrease in carbon dioxide will also lead to a decrease in temperature, the resistance between the two sensors changes. This triggers a “purge” from the CO2 tank, lasting until the chamber reaches the pre-programmed set-point. Unfortunately, incubator temperature settings and humidity levels also affect thermal conductivity sensors, so there is some level of inaccuracy; especially true when incubator doors are opened frequently. With an open door, not only is CO2 lost, but the relative humidity level goes down. Thus, thermal conductivity monitoring incubators are better suited for longer-term storage of cell cultures.
A more accurate (but also more expensive) CO2-level monitoring system is infrared (invisible energy with wavelengths longer than visible light). An optical sensor, measuring light absorption in the infrared spectrum, looks for the amount of carbon dioxide in the incubator; the degree of absorption is proportional to the amount of CO2. The absorption is not affected by temperature or humidity, so it is a more reliable CO2 concentration indicator than thermal-conductivity sensors. Most instruments have a self-contained sensing module, which is auto-calibrated at set intervals. Despite the drawback of higher cost, IR sensing units are the ideal solution when frequent access to contents within the incubator is required.
Final Thoughts
Sourcing basic lab instrumentation such as incubators may seem straightforward, but advanced equipment features that increase functionality call for careful scrutiny. Equipment must be application-appropriate. In regards to selecting an incubator that can control CO2 levels within the chamber, consider the species to be researched, as well as the type of gas detector. If you choose an incubator with CO2 control, you’ll also need a steady supply of gas canisters. Click here for more information about incubators offered by Terra Universal.